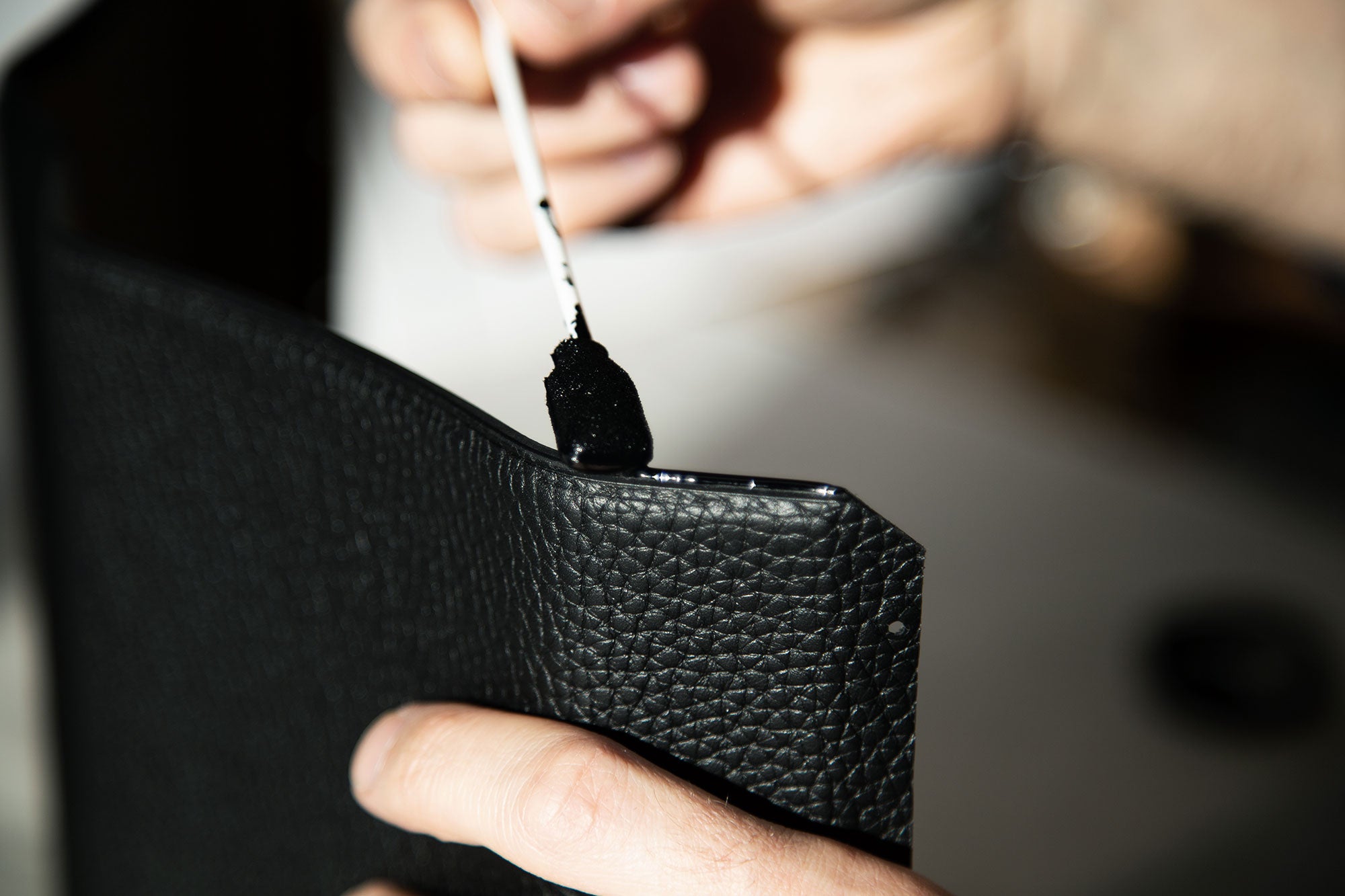
An art meant to be felt - An interview on leatherworking with Thomas Doucet Lupien

For Thomas, product developer and leather craftsman at Charles Simon, the joy of leatherwork lies in the gratification that comes from the process of using premium materials to actualize an abstract idea into a finished, tangible product. We sat down for an interview with the expert artisan to discuss the art of leatherworking, his creative process and the unique blend of traditional craftsmanship and advanced technology in his work environment at the luxury watch and travel accessories designer Charles Simon.
— Let us begin with the basics, what draws you to leather in particular as a material to work with?
—Quality seems to play a particularly important role when it comes to leather and leatherwork. How do you identify top-level leather? For the material itself, it is vital to conduct the quality check by actually touching the leather, feeling its surface and getting a sense of its palpable properties. Another factor to consider is its place of origin. There is a long tannery tradition in Europe, so a lot of the premium leather comes from there. For example, the young bull leather I work with at Charles Simon is sourced from a family-owned tannery in the south of France that was founded in 1927. It really is working with such refined materials that constitutes the pleasure of leatherworking. —What kind of decisions do you make when processing such high-end material? The decisions I make on the daily are all linked to transferring ideas into reality as well as possible. So generally speaking, all decisions revolve around turning the abstract into something concrete. In order to achieve that, a lot of aesthetic and technical verdicts need to be made concerning material specificities or technical details. These judgements require extensive savoir-faire but there are always new problematics that arise and need to be tackled through trial and error. —Can you talk a bit more about your background and the path that led you to leatherwork? I have always been interested in visual art of all kinds and actually studied graphic design with a focus on packaging. But I realized that I had this deep need for tactile labor and longed for the feeling you get from working with your hands. So, I decided to complete 3 years of studies in leatherworking. After graduating I was self-employed for two years, creating for myself and others, before leaving for France to work in product development for Louis Vuitton. At that stage, I really wanted to go to France in order to further my leather crafting education and hone my technical skills. Working in the French luxury industry was the perfect setting for that purpose because it was like starting from scratch and facing a completely new level of challenges. The industry’s cycle of continuous production and pursuit of heightened refinement never stops, which is very stimulating and time-consuming and I appreciate those experiences because they enabled me to vitally expand my expertise and equipped me with the know-how that took me to Charles Simon. —What do you enjoy most about the leatherwork you do at Charles Simon? I really take pleasure in being in charge of the entire production process, from ideation to manufacturing. Because everything is handled internally at Charles Simon, I have a lot of liberty and agency in terms of the production process, which I really appreciate. Additionally, I always savor the manual labor, the touch of the leather, the satisfaction derived from creating something with my hands. It really is less about the finished product itself and more about relishing the creative journey to get there. — What initially inspires you to begin that journey of creation? Inspiration feels very instinctual to me so it is difficult to trace back exactly what it is that inspires me for certain projects. But I would say that in general, everything you see, all the impressions you get from the outside world and all of your experiences feed into your subconscious and influence the creative process on a subliminal level. So I immerse myself in a creatively stimulating environment and absorb a lot of content in my personal life, ranging from paintings to architecture and fashion. I’ve always been drawn to visual art and I think that this input subconsciously sustains my creative intuition. — Can you walk us through the process at Charles Simon from inspiration to holding the finished product in your hands? It all starts with brainstorming and listing possible characteristics of the new product. This sets off the stage of pure creation, which is very instinctive and free at first. We try not to impose any restraints on our imagination and have a lot of open team discussions that involve bouncing ideas off of one another, creating a huge amount of sketches and challenging each other’s concepts. In general, the entire creation process is a team effort that is kept up by the merging of all group members’ creativity and expertise. In this developing stage, it is important to be conscious of contemporary clients and their needs in order to identify what kind of product could add value to their lives and how that can be integrated into the broader vision of the brand. Once a more concrete product idea and design has been established, we move into the phase of figuring out how to actualize our idea and identifying technical problems. The advantage of Charles Simom is that we do everything in-house, which means that we have the chance to manufacture anything we require ourselves instead of being limited by the availability of ready-made parts. This gives us the liberty to develop products that aren’t based on anything that already exists, which is rather rare for a start-up brand. Engineering expertise enables the company to technologically advance craftsmanship in ways that wouldn’t be possible otherwise while the tactile qualities of the natural materials and the long tradition of craftsmanship add a tangible sensuousness to the products. So, there really is no hierarchy between engineering and craftsmanship and the two work together in synergy. The mixed group composition of engineers and artisanal craftsmen is quite uncommon in the industry and creates a unique work environment at Charles Simon. — What project have you worked on that was particularly interesting or rewarding? The development of the watch stand was a really interesting process since there were not many references of similar products to work with and we thus wanted to break through and innovate. The ideation stage of creating a completely original product was very enjoyable and the developing phase was quite technically challenging because it involved applying leatherworking to an entirely new product type. Seeing the result felt satisfying because the watch stand truly embodies Charles Simon’s distinctive merging of engineering and leatherwork. — What motivates you to keep creating? Making things with my hands is extremely gratifying. Especially in an age where people are looking for meaning in their work, artisanal trades provide that satisfaction of having created a concrete thing and seeing the result of your work at the end of the day. It is a lot less abstract than computer work for example, and it is the sense of fulfillment I get from this tangibility that compels me to keep going. It’s also very motivating to notice my personal progress. When it comes to leatherworking, you really never stop learning and there always is room for improvement and ways to refine your skills. — What message do you convey through your products? I actually am not too attached to products in general, which might seem contradictory at first but for me it really is the pleasure that comes from using items in everyday life that counts. I have an appreciation for well-made products that are durable and meant to be used for a long time. To me, the joy of luxury products is derived from integrating them into your life. So the products I make are made less for their luxurious materiality in itself and more in order to support and elevate clients’ everyday lives. — Where do you see the leatherwork industry going in the future? Compared to other trades, leatherworking is a craft that has remained rather close to its traditions and to me, it is the material that is most enjoyable to work with. However, I think a major challenge leathercraft is facing is the need to remain curious and open to new techniques and even to new materials. I like the idea of using know-how from leatherwork in order to support and elevate new materials. For now, leather remains my preferred material choice and I don’t think that anything will be able to beat its touch and sensuousness anytime soon, but I also believe that it is important to continuously look for new ways to improve and push boundaries in order to keep creating in the best way possible. Written by Elizabeth Hanisch